格特拉克(江西)传动系统有限公司是德国格特拉克(GETRAG)集团与江铃汽车集团(JMCG)强强联合,于2007年1月在江西南昌正式投入运营。公司下辖四个工厂,分别为两个南昌工厂、赣州工厂、于都工厂,主要产品为先进的手动及自动变速器,截至2013年变速箱总产能 114万台,员工超过4000人。
格特拉克(江西)传动系统有限公司赣州工厂,赣州工厂占地面积438.46亩,总投资11.89亿元,厂房面积6万多平方米。工厂现有员工1273多人,其中工程技术人员200多人。公司拥有世界一流的齿轮加工和变速器装配生产线,共有各种设备1100台,其中45%的设备从国外引进,已形成年产60万台变速器的制造能力。
设备问题,首当其冲
TBM 与2013年开始帮助格特拉克(江西)传动系统有限公司赣州工厂实施精益转型。
客户为典型的机加工行业,设备密集型企业,而且近一半(45%)设备属进口的高精尖设备,设备不仅是及时完成生产计划的保障,更是产出高质量产品的保障。然而在实际生产运行中,设备问题成了工厂突出的问题,设备故障停机少则几天,多则几个月,主要设备平均OEE不足70%。另外公司维修人力和能力不足,天天面临着救火的局面,设备故障需要排队等待维修。公司虽在进行个别的TPM活动,但是效果甚微,而且也未与OEE的提升联系起来。因为设备问题,常造成生产计划变更,库存增加,制造周期长。工厂管理层也意识到要实现稳定生产,设备问题首当其冲。
共同协作,有效推进TPM
针对客户现状,TBM和客户决定选择一台故障率高的关键设备(滚齿机)进行TPM改善。过程中运用突破改善法(SKB)指导客户的跨部门团队进行了为期一周的TPM突破改善。后续客户以此为模板将TPM 改善扩展到其他重点设备。在改善活动中跨部门的团队团结合作,实施了以下改善措施:
- 历史故障汇总,柏拉图分析,重点故障原因分析和对策实施(包括现场整改,纳入AM/PM计划等)。
- 通过设备点检,清洁检查发现问题46项,当周对问题进行集中整改,消除设备的强制劣化,并润滑清洁更换备件等使设备恢复到自然劣化状态。
- 优化AM项目,并在现场做目视化(插图),培训员工,并用记录表跟踪。
- 优化PM项目,通过分析历史故障,过去的PM记录及参考设备手册,对现有的PM项目进行优化。
- 制作一点课,充分利用员工的智慧,把点检/调整等诀窍点、重点用一点课的形式整理出来,用于对员工培训。
- 制作故障处理手册,通过总结过往历史故障,对典型的故障制作故障处理手册,供维修工学习和解决问题参考。
- 建立设备表现目视跟踪表,利用蓝标签和问题措施纠正记录表追踪问题的解决。员工日常发现的问题不能及时解决的,在设备的问题点挂上醒目的蓝标签并记录跟踪。另外定期对设备表现指标(停机时间,停机次数,OEE)进行定期总结分析,制定改善计划。
可见证改善成果
通过跟踪设备的停机表现,每个月的停机次数如下面的趋势图所示,停机次数从14年开始有了大幅的下降,从13年下半年平均4.5次/月降到14年平均0.6次/月。
滚齿机设备月停机次数跟踪表
另外通过TPM 活动的培训和开展,公司各部门员工意识到了全员参与的重要性,公司还成立了由多部门组员组成的TPM推进小组,TPM活动正在有序有效的展开。
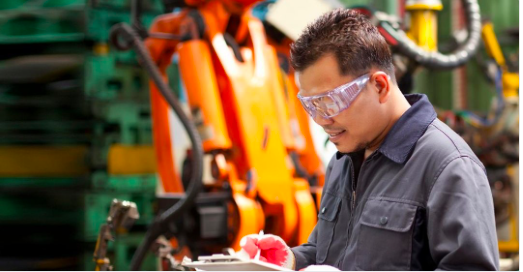
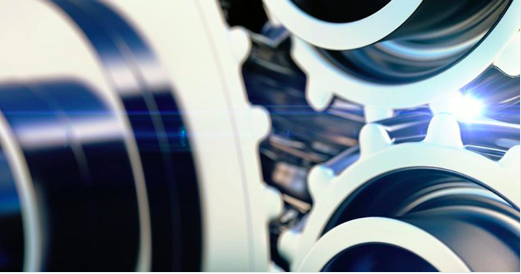